●物流基礎
デバンニングとは?|物流基礎

この記事で分かること
- デバンニングとは何か?
- デバンニングの課題は?
- デバンニングを効率化するには?
一般的に過酷と言われている「デバンニング」。
危険な作業でありながら、時間制限の中でミスのない、丁寧な作業が求められます。
人手不足が深刻化し、生産性が上がらないと頭を抱える企業も多いかもしれません。
そこで本記事では、デバンニング作業員の労働環境を整理し、企業が導入できる対策を解説していきます。
作業員の負担を減らせる環境づくりの参考にしてください。
目次
デバンニングとは?
「デバンニング(Devanning)」とは、貨物をコンテナから取り出す作業のことをいいます。コンテナへの積み込み作業を表す「バンニング(Vanning)」の対義語で、物流業界ではよく使われる言葉です。
一般的には荷主または代理人が直接行う場合と、委託を受けた物流事業者が行う場合があります。
荷主企業がデバンニングを行う場合、基本的には以下の流れで行います。
1.コンテナが作業場に到着する
2.扉を開けて荷下ろしを始める
3.荷下ろしが完了した後に、コンテナ内を清掃する
デバンニング作業は、貨物を「パレット(フォークリフトなどの機械で貨物を運ぶための台)」に積んでから移動させることが一般的です。複数の作業員でパレットに貨物を積んでいき、一つのパレットに既定の数量を積み終えたら、フォークリフトでパレットごと貨物を運びます。複数の作業員でパレットに貨物を積んでいき、一つのパレットに既定の数量を積み終えたら、フォークリフトでパレットごと貨物を運びます。
作業の様子を見たことがない方からすれば、「単純にコンテナから貨物を降ろすだけなら、簡単な作業なのでは?」と思われるかもしれません。
しかし、多くのデバンニング作業現場は過酷な労働環境です。高温になりがちなコンテナ内でパレットへの荷積み作業を行うためには、かなりの体力を必要とします。
デバンニング作業員が置かれている状況
物流部門の担当者は、現場で働く作業員の置かれている状況や労働環境の改善策を求められる場面もあるのではないでしょうか。
ここでは、自社でデバンニングを行う際の課題を整理していきます。
時間に追われながら作業をしなければいけない
一般的にデバンニング作業に2時間以上かかってしまうと、コンテナ輸送車の待機料金が発生します。そのため、コンテナが到着してから原則2時間以内に作業を終わらせなければなりません。
デバンニング作業員は、貨物の落下などを防ぐために丁寧な作業を求められる一方で、タイムリミットに追われながら作業をしなければならないのです。もちろん、輸送車の運転手が手伝ってくれるなどといったことはありません。
また、デバンニングは貨物の取り出しだけではなく、コンテナ内の清掃も作業に含まれます。作業後のコンテナが汚れていた場合、清掃代を請求されてしまう可能性があるため、清掃を含めてすべての作業を2時間以内に終わらせる必要があります。
作業員の労働環境が過酷になりがち
デバンニングは、基本的に手作業で貨物を下ろしていく作業のため、危険と隣り合わせです。
高い場所に積まれた貨物を下ろす際には、貨物の上に乗って作業を行うことも多いので、作業員の落下事故のリスクがあります。
また、コンテナ内は空気の流れが無いため熱気がこもりやすく、夏場は50℃以上もの温度に達することがあります。体温をはるかに超える温度の中で作業することになるため、熱中症にかかるリスクも懸念されます。
このような環境起因による危険性があるだけでなく、そもそも重い貨物を手作業で移動させるだけでも非常に過酷です。そのため、作業員は常に腰痛などを引き起こすリスクを抱えています。
商品が破損してしまう可能性がある
貨物が輸送される際、コンテナ内で荷崩れが発生している場合があります。これにより、コンテナ開扉時に貨物が落下し、商品を破損させてしてしまうトラブルが多く発生しています。
また、落下した貨物が作業員に当たってケガを負ってしまう可能性もあるため、コンテナの扉を開ける動作一つにも、十分に気を配らなければなりません。
加えて、高所での荷下ろし作業も多いため注意が必要です。特に、貨物の上などの不安定な足場で作業をする場合、少しバランスを崩しただけで貨物を落下させてしまうことがあります。低い場所での作業に比べ、高所からの落下となると商品へのダメージは甚大です。
商品を破損させたことによる賠償請求に対しては保険が適用されるとはいえ、関連会社との信用問題に発展しかねないため、作業員には慎重な作業が求められます。
デバンニングの作業効率を高めるには環境づくりが必要
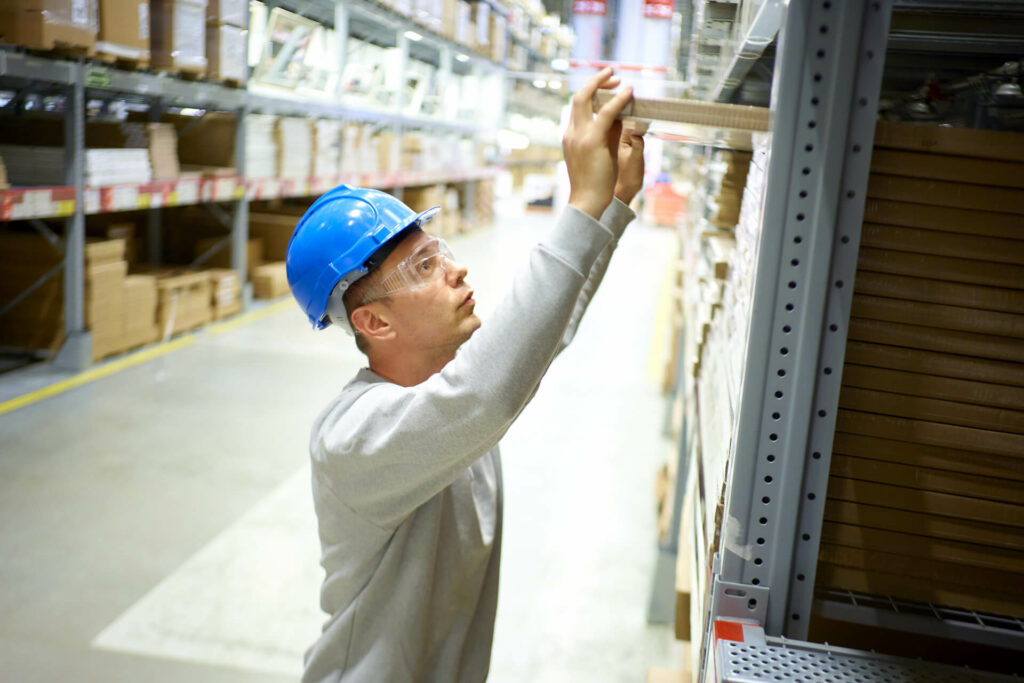
デバンニングの課題を解消するには、まず作業しやすい環境を整えることが重要です。以下に環境づくりのポイントをまとめたので、ぜひ参考にしてください。
①作業員の安全を確保する
まずは安全靴や作業着、ヘルメットの着用を徹底させましょう。当然のことのように思えますが、きちんとルール化して着用を徹底させる環境をつくることが重要です。
また、夏場の暑さ対策として、エアコンが使えない環境で働く作業員向けに、空調服や冷却ベストを導入するのもおすすめです。
さらに、コンテナを冷やすといった工夫も有効です。例えば、コンテナの屋根にスプリンクラーを設置して気化熱で温度を下げたり、遮熱シートを設置して熱の侵入を防ぐ方法があります。
コンテナ冷却システムの提供会社によると、コンテナの屋根にスプリンクラーで散水することで50℃以上あったコンテナの表面温度が30℃台まで低下したという実測結果が出ているようです。コンテナ用遮熱シートも有効性が示されており、設置するとコンテナ内の温度が10℃以上も低下することがあります。これらのシステムや備品を有効活用し、作業員の熱中症リスクをなるべく軽減させましょう。
②動線とレイアウトを調節する
動線は作業員や商品が移動する流れを指し、レイアウトは置き場などの配置を指します。
基本的にデバンニングは手作業で荷下ろしを実施し、フォークリフトで荷物を倉庫内の保管場所まで運ぶため、各工程間を最短で結ぶ動線の設計が理想です。
不必要に長い動線は時間的なロスの原因となり、狭い動線は接触事故を招くなど、動線を意識していないレイアウトは作業上のリスクを高めてしまいます。
このように動線やレイアウトは、作業効率ためだけではなく事故を未然に防ぐ役割もあることを覚えておきましょう。
具体的には、フォークリフトと作業員が同じ通路を通るような動線や、デバンニングを行う場所から荷物の保管場所までの距離がかけ離れているようなレイアウトは見直しの検討をおすすめします。
③作業場の高低差をなくす
作業場に高低差があると、作業員のケガや商品の破損リスクが高まります。そのため、なるべく輸送車と同じ高さに作業場を作ることで、大幅にトラブル発生リスクが軽減されます。
また、高低差をなくすことで作業効率も上がるため有用な方法です。
高低差をなくす方法としては、バンステージを設置することが効果的です。バンステージとは、コンテナやドレー車の段差分に設置して、高低差を解消できるスロープのことをいいます。
バンステージを活用することにより、コンテナから手作業で荷下ろししていた貨物を、フォークリフトで直接運搬することが可能です。これにより、フォークリフトをフル稼働させて荷下ろしが行えるため、作業スピードが格段に上がります。それと同時に、パレットへの荷積み作業が不要となることから人手不足の解消にもつながり、ひいては輸送コストの削減も期待できます。
デバンニングはロボット技術の活用が進んでいる
このようにデバンニングの作業効率を上げるためには、作業員が安全に作業ができる備品や設備をそろえたり、倉庫内の環境を整えることが重要です。
しかし、中には作業員の高齢化が進み、新たな人材もなかなか定着しないとお悩みの企業担当者の方もいるのではないでしょうか。
ここで知っていただきたい点は、デバンニング作業は「人が行う作業」から「ロボットが行う作業」に代替えできるということです。
様々な業界においてAIやロボットの導入が進められており、最新のテクノロジーによって課題解決して新しい価値を生み出していくことを「DX(デジタルトランスフォーメーション)」といいます。昨今では物流業界におけるDXも急速に進んでいます。
実際にロボットを導入している現場では、コンテナ内の貨物を下ろす位置までコンベアとともにロボットが自動走行し、コンテナ内が空になるまで奥に進みながらアームを使用してデバンニングを実施するといったことが可能になっています。
つまり、コンテナが到着してから貨物を倉庫内に移動させるまでの流れを、全てロボットだけで行えるのです。
ロボットが人に代わり作業を行うことで、前述したデバンニングにおける課題はかなり改善されます。作業員の負担が大幅に軽減されるためケガなどのリスクが減るだけでなく、作業にかかる時間や人員も削減できます。
さらには貨物の損傷リスクも大きく抑えられるため、デバンニング現場へのロボット導入メリットは絶大です。
近い将来、あらゆるデバンニング現場においてロボットは不可欠なものになっていくでしょう。
デバンニングのソリューション
実際デバンニング作業を効率化するためのソリューションは、どのように見つければよいのでしょうか。
大きく分けて2つの機器の利用があげられます。
デバンニングロボット
一つ目は、コンテナからの荷物の移動をロボットを活用する方法です。
自動フォークリフトのように、一つひとつの荷物の下にアームを差し込んで持ち上げ、そのアームを180度方向転換してコンテナから取り出すロボットです。作業位置まで自動走行し、画像認識システムで荷物を判別して取り出します。
伸縮式ベルトコンベア
もうひとつが、伸縮式ベルトコンベアです。
上記のデバンニングロボットは、コンテナから荷物を取り出すところまでしかできません。
その先、倉庫内に荷物を運び入れるには、ベルトコンベアが必要となりますが、トラックの荷室の奥のほうの荷物を取り出す際には、デバンニングロボットの位置に合わせてベルトコンベアも伸縮する必要があります。そのため活用されるのが「伸縮式ベルトコンベア」です。
まとめ
本記事ではデバンニングの基礎知識や、デバンニングを行う労働環境の改善方法について紹介しました。人手不足が叫ばれる中、有効な改善策を講じるためには作業員の現状を理解する必要があります。
デバンニングは、基本的に手作業で荷下ろしを行うため過酷です。また、高所・高温な環境下での作業となることも多いため、作業員の落下事故のリスクや熱中症にかかるリスクをはらんでいます。しかしながら原則2時間以内で作業を終えなければならないため、時間に追われながら作業をしなければなりません。
このような現場環境を改善するためには、動線とレイアウトを調節することや、備品・設備を導入することが求められます。特に、コンテナとの高低差をなくすためのバンステージ設置は非常に有効です。
バンステージを活用すれば作業効率が格段に上がるだけでなく、作業員の手作業が軽減されることにより人手不足の解消にもなります。
また、ロボット技術の導入も有効です。ロボットが人に替わって作業を行うことで、バンステージの導入より直接的に人員削減につながります。
あらゆる産業の業務が自動化されていく中で、リスクの多い現場にこそ積極的にAIやロボットなどのテクノロジーを導入していくべきだと考えます。
ご相談・お問い合わせ
物流最適化に関する個別相談を、ご紹介・信頼ベースで少数受けています。
初めての企業様はこちらのフォームよりご連絡ください
人気キーワードで検索