●物流基礎
誤出荷対策はどうする?作業別の原因から改善ポイントを探る
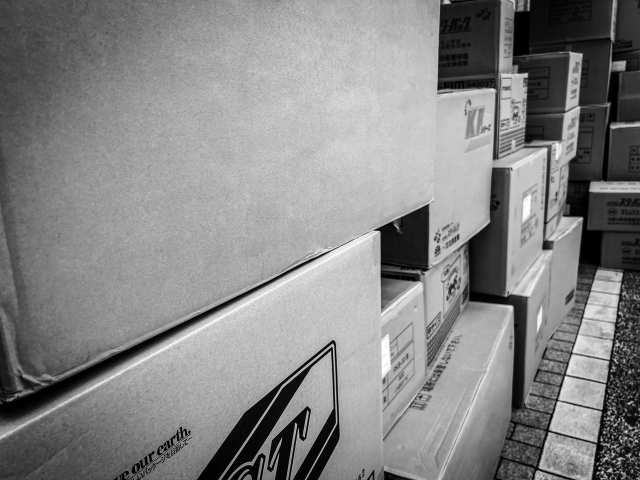
この記事で分かること
- 誤出荷はなぜ起きるのか?
- どうしたら誤出荷を防げるか?
「注文したものと違う商品が届いた」という誤出荷に対するクレームに頭を悩ます倉庫管理者の方もいるのではないでしょうか。
倉庫内の作業員は、限られた時間の中で細かな出荷作業を行うためミスが起こりやすいものです。そのため管理者にはどの作業で誤出荷の原因が発生しやすく、どのような対策を講じるべきかを把握する必要があります。
この記事では、誤出荷の原因や効果的な対策について解説します。
目次
誤出荷とは?
商品を出荷するまでのプロセスの中で、商品自体や商品の色やサイズや数量、発送先などが誤った状態で出荷されてしまうことを「誤出荷」と呼びます。
近年、IT技術を導入し出荷プロセスを自動化する動きも見られますが、ピッキングや梱包などを未だ手作業で行なっている企業もあります。人が行う以上は、ヒューマンエラーをゼロにすることは極めて困難ですが、「誤出荷」は顧客に迷惑をかけ信用を失うだけでなく、社内のクレーム対応工数が増加するといった影響範囲は少なくありません。
※顧客からの返品など、通常のロジスティクスと逆の流れで商品が戻ってくる「リバースロジスティクス」に関しては、こちらの記事で解説しています。
「リバースロジスティクス」へリンク
「誤出荷」の原因は、[1]誤品、[2]誤数、[3]誤発送の3つに分けられます。それぞれ、詳しく解説していきます。
[1] 誤品
注文商品と異なった商品を出荷してしまうことを「誤品」と呼びます。ピッキング時に品番の見間違いや、色やサイズなどの確認不足などシンプルなミスに起因します。他にも、商品タグの貼り付けミスやピッキングリストの作成ミスなど、ピッキング作業前の段階でミスが起きることもあります。
[2] 誤数
2個の注文に対して誤って3個出荷するといった、注文数と異なる品数を出荷してしまうのが「誤数」です。色違いで「ブラックとホワイトを1個ずつ」という注文に対し、ブラックだけを出荷した場合も誤数とみなされます。
[3] 誤発送
配送すべき宛先とは異なる第三者へ発送してしまうのが「誤発送」です。伝票の貼り間違えで起こる場合が多いミスですが、「誤発送」は注文者・誤発送者の両者に迷惑をかけるだけでなく、個人情報を漏洩することにもなるので、大きなリスクを抱えています。
誤出荷の中でも注意したい「テレコ出荷」
「テレコ出荷」とは出荷先を間違えてしまう[1] ことを表す言葉で、本来A社に発送すべき荷物を、誤ってB社に発送してしまい、B社に発送すべき荷物をA社に発送してしまうミスのことを指します。テレコには「あべこべ」や「食い違い」という意味があり、元々は歌舞伎の二つの異なる話を一つの脚本にまとめ、交互に進行させることが由来となっています。
テレコ出荷が発覚するのは、顧客の元に商品が届き、開封したときがほとんどです。このため、テレコ出荷が発生すると顧客のクレームにつながり、ひいては顧客の信頼を損なう結果となります。
従来発送すべきであった元々の発送先と、誤って送付してしまった送付先の2か所に対してお詫びや対処が必要となり、ミスへの対処も影響範囲が大きくなります。
誤出荷によって発生する経営リスクについて
このような誤出荷は、顧客に迷惑をかけるだけでなく、企業の信用も傷つけかねません。ここからは、誤出荷が引き起こす経営リスクについて掘り下げます。
個人情報の漏洩
誤発送は、第三者の手に注文者の個人情報が開示されてしまいます。BtoB取引の発送の場合は、納品書や伝票に注文内容・価格などが記載されているため、企業の取引内容まで開示されることを意味し、大きな企業間トラブルに発展するリスクをはらんでいます。
取引先との信頼関係が崩れる
誤発送が発生すると、発送元企業への信用は低下します。場合によっては、取引を取りやめる顧客が出て来るかもしれません。一度崩れた信頼関係の再構築は容易ではなく、時間と労力がかかります。誤発送が多発するような場合は、リピート顧客が定着せずに、企業の売上に直接的な影響を与えかねません。
在庫差異
在庫差異とは、帳簿・システム上の在庫数と、実地棚卸で確認できる在庫数に差が生じることです。商品を10個発送すべきところを20個発送してしまう誤出荷が発生すると、10個分の在庫差異が生じ、売上が損失されます。
その差異が発生したまま、他の顧客からその商品を受注すると、あるはずの在庫がなく販売の機会を損失するだけでなく、発送が遅れて顧客に迷惑がかかります。社内では、原因究明、在庫照合、商品の捜索のための棚卸などを強いられることになります。
誤出荷の発生要因
誤出荷が起きやすい工程は、[1]出荷指示、[2]ピッキング・仕分け、[3]配送、の3つです。
それぞれ詳しく解説をしていきますが、まず前提として、誤出荷の多くは、複数の原因が重なって発生することを念頭におきましょう。3つのどれかが解決しても、直ちに誤出荷がゼロになるというわけではありません。
また、この3つの工程の多くが人の手を介して行われるため、誤出荷の多くがヒューマンエラーに起因することも認識する必要があります。発送業務の現場でヒューマンエラーを100%なくすことは不可能です。
このような点を踏まえた上で、どのような対策が効果的なのかを考えましょう。
誤出荷の原因・対策|1. 出荷指示
まずは、出荷指示をする際の誤出荷の原因と対策です。
情報の入力ミス
ピッキング指示書作成時の入力ミスは誤出荷の直接的な原因となります。また商品入荷時に、誤った商品情報を登録し誤った商品管理タグを貼り付けると、後日出荷する際、その誤った管理タグで作業されるので、ミスに気がつかないまま誤出荷してしまいます。
このような情報の入力ミスを防ぐためには、入荷時から出荷時までの商品管理ができるWMS(倉庫管理システム)を導入し、ピッキング指示書や商品管理タグへの手入力を減らすことが有効です。
ロットの指定ミス
同一商品が同一顧客にリピート購入された場合に、前回出荷した商品よりも古い商品を発送してしまうのも誤出荷の一つです。特に賞味期限や消費期限がある食品などの場合は「在庫管理ができない企業」として、信用を失いかねません。製造ロットごとに管理している場合に、出荷するロットの順番を誤って発送することが原因です。予防策としては、ロットをWMSでシステム管理し、前回出荷時より古いロットを出荷指定するとアラートを出すなどの運用が効果的です。
誤出荷の原因・対策|2. ピッキング・仕分け
次に、ピッキング・仕分け時について確認しましょう。
類似商品のピッキングミス
商品名が同じでも色やサイズ、容量などの規格が違ったり、パッケージが違ったりする類似商品がある場合は、ピッキング作業時の対策が必要です。
例えば、倉庫の棚割りを容量順に整理し、ピッキングリストも容量順に作成すれば、作業者の勘違いが少なくなります。商品コードにも枝番などで細かな分類を行うことで、システム的にも差異を持たせるといいでしょう。さらに作業者の判断のみに頼らず、注文データと照合するためハンディスキャナーを導入することも効果的です。
商品の数えミス
ピッキング作業時に最も多いミスが、数え間違いです。注文通りの数量をピッキングするためには、指示書上の工夫が欠かせません。注目すべき数量は、色や文字サイズを変えて表示するなど、作業者が気付きやすい書式で作成しましょう。
チェーン店への納品で複数店舗に商品を仕分ける際は、ピッキングリストの内容が同じで数量だけが異なることが多く、見間違えやすくなります。各店舗への仕分け後に、注文データと照合するエラーチェックができれば安心です。
同梱商品の入れミス・入れ忘れ
複数の商品を1つの注文として同じ箱に梱包する際も手作業になることが多く、うっかり入れ忘れてしまうと誤出荷になります。ピッキングリストの読み飛ばしや、梱包時のチェック漏れなどが主な原因です。
梱包する前に商品が揃っているかハンディスキャナーで検品したり、ピッキングリストを指差し確認するなどの対策が必要です。
誤出荷の原因・対策|3. 配送
最後に、配送時にも誤出荷の原因が潜んでいます。
配送伝票の貼りミス
注文商品が梱包されたら配送伝票を貼り付けます。ここで配送伝票を取り違えて貼ってしまうと重大な誤発送が起きてしまいます。ピッキングリストと伝票を別々に保管して伝票を貼り付ける際に、宛先を確認をしなかったのが原因です。
このミスを防ぐには、配送伝票とピッキングリストは必ず一対にして、ピッキング作業に取り掛かることが重要です。また、ハンディスキャナーで、ピッキングリストと配送伝票を照らし合わせエラーチェックできる環境を構築できると安心です。
住所などの宛先ミス
配送伝票を作成する際の手作業は誤出荷につながります。システムから配送伝票をプリンターで印刷することで、ヒューマンエラーを削減することができます。
ただし、顧客からの急な配送先変更の連絡があった場合は要注意です。伝票発行前なら直ちに注文情報を訂正すれば良いだけですが、発行後は配送伝票を回収し、差し替える必要があります。この差し替えが正確に行われない場合は、間違ってピッキングしてしまい、別住所へ重複して発送することになってしまいます。
積み下ろしミス
ドライバーが誤った納品先に荷物を下ろしてしまうこともあります。これはドライバーの確認不足から来ることがほとんどです。複数個口の発送では、複数個あることを分かりやすく伝えられる表示を行いましょう。またトラックに積み込む際に、納品先の確認・配送指示を明確に行い、ドライバーが迷わないようにしましょう。
納品先でも受け取る際に検品を行ってもらうように依頼して、下ろし忘れがないか納品伝票と付き合わせて検品を徹底することも大切です。
誤出荷を数値化して改善計画の基準を決めよう
誤出荷の発生率を可視化するために算出される「誤出荷率」には、PPM(パーツ・パー・ミリオン)という単位が用いられます。これは「100万分のいくらか」という割合を示す指標ですが、具体的な算出方法は以下の通りです。
誤出荷率(PPM)=誤出荷発生件数÷作業件数×1,000,000
例えば、誤出荷発生件数が5件、作業件数が10万件の場合は50PPM(5件÷100,000件×1,000,000=50PPM)です。
目安として100PPM以下が望ましいとされますが、中には「10PPM以下」など、より高い目標設定をしている企業もあります。大切なのは、自社の誤出荷率を正確に把握し、適切な改善計画をたて、改善したかどうか継続的に効果測定を行なっていくことです。また、社内全体の課題として目標の達成状況を共有していくことも欠かせません。
企業が誤出荷対策としてできる取り組み
誤出荷を防ぐための対策検討時には、以下の3点を意識すると良いでしょう。
業務ルールを定め、共通の手順で作業を進める
システム導入により作業がシステマチックになったとしても、そのシステムを運用する際にエラーは発生するものです。また倉庫内でのロケーションのルールなど、基本的なルールは作業者が正しく理解している必要があります。業務ルールを明確に定め、誰もが理解できるマニュアルとして明文化されていれば、経験の深浅に関わらず作業者全員が共通の手順で作業を行うことができ、ヒューマンエラーの削減につながります。
エラーが起きた際は再発防止のためにも、改善策をマニュアルに反映して全体共有することが大切です。改善策が全体共有されずに作業が属人化していると、誤出荷の原因究明が難しく時間がかかる上、改善策を打ち出しにくくなります。
現場の声を吸い上げる
ミスの軽減には、現場の声を拾うことも大切です。誤出荷対策作業者が困っていること、こうだったら良いなと感じていることを直接ヒアリングし、誤出荷予防の対策のヒントを探ってみましょう。
ただし、現場が感じる課題とデータ分析により見出された課題が必ずしも一致するとは限りません。現場の意見だけを取り入れるのではなく、管理者・経営者層が広い視野に立ち、現状把握と改善策の検討を行うことが大切です。
作業場のスペースを拡大する
出荷作業では、適度な作業場のスペースを確保することも誤出荷予防に有効です。作業中は、大量の商品、ピッキングリスト、外装箱、同梱資料と、モノに溢れます。狭い作業場では整理整頓が難しくなり、商品が隠れたり、同梱すべきものを入れ間違えたりしやすくなります。作業に必要なスペースを確保しましょう。
倉庫内作業はWMSに任せる時代に
上記のような対策を行なっても、ヒューマンエラーをゼロにするのは難しいため、近年では、倉庫内業務を自動化する「WMS(倉庫管理システム)の導入」が誤出荷対策の最も有効な手段として注目を浴びています。
WMSの導入により、ロケーション管理や入出庫・在庫の管理、納品書の作成を自動化でき、ピッキング指示書と現物の目視による照合作業など、人を介した作業自体をなくすことができるので、ヒューマンエラーによる誤出荷を防止することができます。
例えばシステムがピッキングリストを正確に出力し、保管場所も教えてくれたり、ハンディーターミナルで入庫/出庫に商品を読み込むだけで検品してくれます。
他にも、ピッキング時に倉庫内の最短ルートを出力や、煩雑になりがちな返品対応の時短化など、作業効率化・平準化につながるというメリットや、在庫の状況をリアルタイムかつシステム上で把握し、生産や仕入の計画策定や人材配置などに役立つというメリットもあります。
AIによる画像認識技術を用いた誤出荷対策
昨今では誤出荷を防ぐ手段の一つに、AIを用いたサービスを提供する事業者が増えています。特にBtoCのECサイトでは、細かな注文に対して正確な商品のピッキングが必要となります。そのようなケースでは、ピッキングロボットが注文商品を自動でピックアップしてくれます。
システムから注文情報が届くと、ピッキングロボットの前にベルトコンベアで注文商品が保管された箱が届きます。ピッキングロボットは、画像処理技術により該当の商品をAIカメラで判別して必要数量ピッキングして別の箱へ移します。この作業を必要商品分繰り返したら、ピッキングした商品の箱を梱包するエリアへベルトコンベアで次の工程へ送ります。
次に、注文情報とピッキング商品が正しいか、こちらも画像認識技術でAIカメラが商品画像と商品コードが合致するか、個数や色が正しいかを確認する検品作業を行います。検品が完了すると出荷用の箱で梱包され、自動で配送伝票が貼り付けられて発送されます。
このような画像認識技術の活用は、ECにおける物流だけでなく、様々なヒューマンエラーが発生するような業態でも活用されています。冷凍食品を扱うようなケースでは、冷凍室内の極寒の環境での作業が発生するため、目視検品のミスや、類似品の多さでピッキング・検品ミスが発生します。また生鮮食品やアルコール飲料は、ロットごとの外箱にはバーコードシールが貼ってあっても、個別商品に貼っていない場合もあり手作業の必要が生じる場合があります。このようなケースも、画像認識術が個別商品を特定してピッキング・検品できるようになったのです。
このように画像認識技術の進歩により、ピッキングや検品作業が自動化が進み、ミスが軽減されるようになってきたのです。
画像認識技術については、こちらの記事で詳しく解説しています。
まとめ
「誤出荷」とは、商品を出荷するまでのプロセスの中で、商品自体や商品の色やサイズや数量、発送先などが誤った状態で出荷されてしまうこと。「誤出荷」は顧客に迷惑をかけ信用を失うだけでなく、社内のクレーム対応工数が増加するといった影響範囲は少なくありません。
注文商品と異なった商品を出荷してしまう「誤品」、注文数と異なる品数を出荷してしまう「誤数」、配送すべき宛先とは異なる第三者へ発送してしまうのが「誤発送」の3種類のミスが「誤出荷」の原因です。
「誤出荷」を対策するには、適切な出荷指示を行う、ピッキング・仕分けによるヒューマンエラー防止策を行う、配送時の伝票ミスやドライバーの管理ミスを軽減するといった対応が必要となります。
基本的にはヒューマンエラーによるミスが多いため、WMS(倉庫管理システム)を導入し、できるだけ手作業を少なくするということが、ヒューマンエラーの防止につながります。
ご相談・お問い合わせ
物流最適化に関する個別相談を、ご紹介・信頼ベースで少数受けています。
初めての企業様はこちらのフォームよりご連絡ください
人気キーワードで検索